Designing Mars at SAM
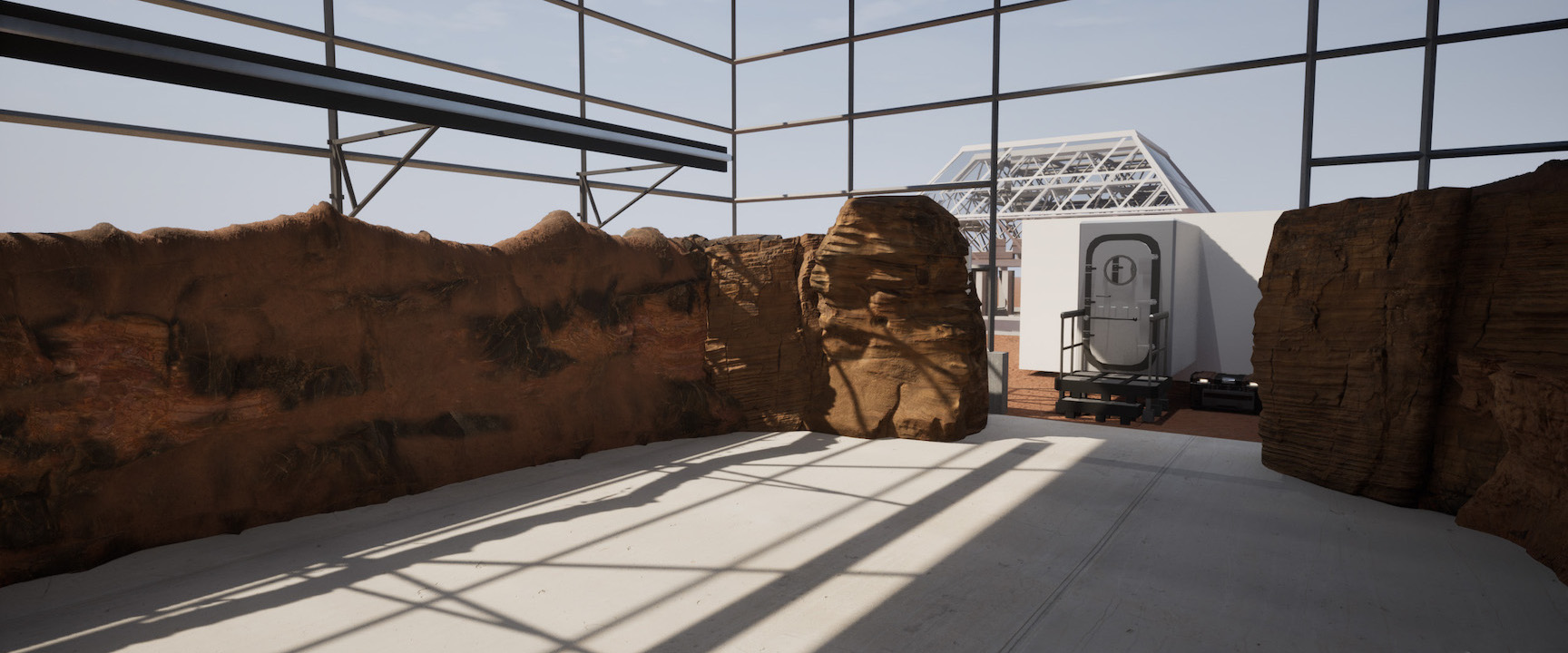
Mars yard at SAM model by Bryan Versteeg | spacehabs.com
In 2023 Kai invited Dr. Jim Bell to visit SAM. Dr. Bell is a world renowned planetary geologist at Arizona State University, School of Earth and Space Exploration, and designer of the ‘Mastcam’ cameras for the Mars rovers Curiosity and Perseverance. They reviewed the then small Mars yard “sand box” filled with crushed basalt, and discussed the ultimate expansion to a 2600 sq-ft facility complete with 10-12 foot high crater walls.
Together they considered three possibilities:
a) Take a single volcanic or impact crater on Mars and shrink it down to something that would fit within 2600 sq-ft. The challenge would be that we’d lose the detail of the features by the very function of miniaturization; or
b) Take a life-size feature such as a cliff band or gully bottom on Mars and recreate it, centimeter for centimeter adjacent to SAM. While this would give visiting crew members a very realistic EVA experience, the shelf-life for our Mars yard would be limited to the relatively narrow set of geologic features in a few hundred square meters; or
c) Build an amalgamation of features taken from various sites on Mars. This final approach results is a bit of a Frankenstein monster but is far more interesting, has a greater shelf-life, and can be modified in the future without geologic ramification.
APRIL 20, 2024
d) With the transition from an intended rebar, lath, and concrete construction medium to carved foam and shotcrete, it became possible to fabricate a realistic assembly of diverse features on Mars in the confines of a single space, and in so doing, build a world in which the represented geological layers tell a nearly complete story of millions of years of construction and erosion. Learn more …
In preparation for the arrival of Red Hen Industries and their Hollywood set construction crews, Kai once again reached out to renowned space architecture visionary Bryan Versteeg (top image) to generate a rough 3D model as a means to visualize the initial parameters of this massive undertaking.
In parallel, ASU School of Earth and Space Exploration undergraduate Tasha Coelho assembled a document that explores the varied types of features that might be represented in the SAM Mars yard geology, building on the initial photographs captured by Matthias Beach in the fall of 2023 with her own deep dive into the NASA and ASU image archives.
The features considered include: anthropogenic features, concretions and buried pebbles, conglomerates, gullies and talus slopes horizontal striations and outcrops, linear color variations, mud cracks, recurring slope lineae ripples, and veins and ventricals.
More than 100 images from the Curiosity Mars rover were studied, two dozen printed and laminated as initial guides for the Red Hen crew.
Concretions
- Clumps of minerals formed when water soaked the rock long ago
- Resistant to erosion
- Some are close to being fully revealed
- Example: Martian Blueberries (Hematite, an iron mineral). These are also found in Utah’s petrified sand dunes. They become superficial (meaning, separate from the stone in which they formed) as surrounding sandstone/mudstone erodes away. These were discovered by Opportunity the same day it landed.
Conglomerates
- Rounded pebbles bound together with varying degrees of round
- Nearby loose pebbles that have dropped out of the conglomerate
- Evidence for fast flowing water; needed to mobilize and round heavier rocks
Horizontal striations
- Buried sand dunes
- Fine grain
- Cross-bedding indicating different flows of water OR whole rock unit moved
- Horizontal Striations
- Fracturing
Veins
- Fluid-rock interactions
- Water carrying minerals and filling cracks in rocks
- More resistant to erosion compared to surrounding rock
- Dark base colors with light features (calcium sulfate aka gypsum}
Ventifacts
- Wind carved rocks
- Wind blown grains erode and smooth surfaces, similar to a sand blaster
- Resulting rock can show prevailing wind directions (learn more)
Recurring Slope Lineae
- From orbit these features appear to be meters wide and kilometers long; might also be seen on smaller scales
- Different theories for formation:
– CO2 sublimation
– Seasonal heating melting sub-surface briny water
– Hydrated clays
– Dry landslides
Anthropogenic features
- From rovers/humans attempting to learn what lies beneath the surface
- Educational opportunity
- Reveals unoxidized layer
Mud Cracks
- Floor features, or on top of flat rocks
Subsurface Water / CO₂ Ice
- Newly revealed subsurface ice imaged by Phoenix and HiRISE
- Have only been observed on the ground, not on vertical outcrops (need to verify)
Gullies + Talus slopes
These are not applicable to the size and scale of the SAM Mars yard.
Water (or CO₂) ice in cold traps
These can only be imaged from orbit, as with Korolev crater.